宝钢烧结工序环保升级改造和四烧结投产实践
近年来,宝钢股份公司一直在进行环保、节能、高效的烧结工序综合改造。在已投产的四烧结和在建的三烧结大修改造工程以及后续工程中,作为长流程钢铁制造工艺第一步的烧结工序,通过自主集成创新实践绿色制造,从而践行宝钢环境经营的理念和战略。
烧结生产工艺流程的再解析
在长流程钢铁制造工艺中,烧结是铁素流在碳素流和能量流作用下进行物理化学变化的第一步,是将铁矿石冶炼成钢铁的繁杂工序的开始。
基于烧结生产工艺流程的特点,分析烧结生产流程的关联度和渗透力可知,烧结工艺须明确3个功能定位———烧结矿生产制造功能、余热能源转换功能、资源综合利用功能,同时,确保3个立足点———资源利用高效化、能源使用节约化、污染物排放最小化,从而明确“高效、低耗、节能、环保”的烧结工艺定位,使烧结工序契合钢铁企业“资源节约型、环境友好型”的发展目标。
宝钢烧结在综合改造实践过程中,通过采用新工艺、新装备和新技术,使得烧结生产工艺流程进一步优化,夯实了烧结工序的3项功能定位和3个立足点。
主要工艺技术与装备的优化
燃料准备。
烧结固体燃料中的碎焦和无烟煤须加工到粒度3mm以下再参与配料。为了满足≤3mm粒级比例≥90%、平均粒度1.2mm~1.6mm和减少无烟煤过粉碎的质量要求,并考虑物流供应能力,烧结升级改造工程设计采用“粗破+筛分+细破”的工艺流程。
四烧结燃料准备系统的设备配置为“对辊破碎机+振动筛(3mm分级)+四辊破碎机”,新三烧结则优化为“可逆双反击锤式破碎机+振动筛(3mm分级)+四辊破碎机”。新三烧结的燃料破碎加工系统考虑二、三烧结共用,并具有向四烧结供料和外排焦粉的功能。新的燃料加工工艺具有流程相对简洁、质量保证能力较高、物流供应能力较大、运行维护量相对较低等特点。
配料与混合制粒。
在配料方面,四烧结和新三烧结分别设置17个、20个配料槽,有效容积有270m3、380m3和450m3等多种规格,以适应烧结生产对各种物料的贮存需求。烧结生产采用重量配料法,以实现稳定精确配料。混匀矿、熔剂、固体燃料、内返矿与高炉返矿的给料方式采用“圆盘给料机+电子皮带秤”,生石灰与内外部除尘灰则采用“星型卸灰阀+螺旋给料机+电子皮带秤”。
在混合制粒方面,宝钢烧结在升级改造过程中形成了“一段卧式强力混合机+两段圆筒混合机”的三段混合制粒工艺,并在引进和消化吸收的基础上,实现卧式强力混合机的国产化,改进规格、排料、结构等设计,以提高可靠性和稳定性。
铺底与布料。
在铺底料方面,铺底料选用的是烧结矿整粒过程中分离出的一定粒级成品烧结矿,其粒度由原来的10mm~20mm优化为10mm~16mm。铺底料厚度可在20mm~80mm范围内调整。
在布料方面,烧结机头部设有混合料组合偏析布料装置,由混合料给料漏斗、圆辊给料机、电磁偏析布料器和辊筛式布料器而共同组成。混合料给料漏斗由漏斗本体和布料闸门组成。布料闸门采用液压控制的“扇形主闸门+微调闸门”形式,以实现烧结机宽度方向均匀布料。圆辊给料机转速可调,与扇形闸门开度调节一并成为给料量调整的措施。电磁偏析布料器是反射板下方安装有可调磁场装置的布料器,辊筛式布料器采用九辊型式,采用9台变频调速电机驱动,倾角为40°可调。
点火与热风回用。
新三烧结配置有一台点火保温炉及热风罩设备。点火保温炉以焦炉煤气为燃料,实行热风点火助燃和保温烧结,采用微负压点火工艺,点火温度1150℃±50℃,点火时间1min~1.5min。点火温度、煤气与空气的比例以及用量均由计算机自动调节。助燃风取自环冷机高温段,分成三路供给点火烧嘴、保温烧嘴和保温罩(保温炉二段),风温经调节稳定在300℃左右。
烧结。
在烧结工序升级改造过程中,持续实施厚料层烧结,并相继提高设计料层厚度。四烧结通过技术攻关,料层厚度由设计800mm提高到实际880mm,工序能耗达到45kgce/t-s(含脱硫)以下。新三烧结初步设计中将台车栏板高度由可研的850mm提高到950mm,设计料层厚度由900mm提高到1000mm,配套采取增加主抽风机负压、提高烧结机台车荷载和轨道等级、加大柔性传动装置输出扭矩等设备措施,采用优化可切换风箱配置等工艺调节手段,为厚料层烧结生产提供条件。预计工序能耗将低于四烧结水平,并可提高烧结矿成品率0.5%。
新三烧结采用加宽型烧结台车,即抽风宽度5000mm、栏板宽度5500mm,加宽部分采用盲箅条结构型式。台车栏板高950mm、车体梁高490mm,台车车体强度得以提高。车轮与轨道接触面轮缘直径和车轮轴向曲率半径适当增加,以减少车轮与轨道间的接触应力。车轮与轴承为整体结构,并采取确保轴承润滑的措施。中部轨道采用日本进口全线淬火60kgN钢轨制作,以减少磨损延长寿命。九辊布料器下部设置四排交错排列的加长高强钢管组成的通气棒装置,可进一步提高混合料透气性。
烧结矿处理。
烧结矿处理包括烧结饼热破碎、烧结矿冷却、整粒筛分、取样检验几个环节。烧结饼热破碎采用水冷轴式单辊破碎机和固定水冷箅板,热烧结饼被破碎至粒度≤150mm,经给料装置进入液密封鼓风环冷机。
液密封鼓风环冷机摒弃传统环冷机的锥面和平面双层密封结构,重新构造了一个由多单元组成的静密封系统和一个以水作密封介质的动密封系统,可实现总漏风率≤10%。新三烧结选用了目前规格能力最大的LSCC-700液密封鼓风环冷机,有效冷却面积700m2,处理量1400t/h,冷却时间约65min。台车栏板高1.6m,宽4m,回转中径63m,配置6台冷却风机。
新三烧结整粒筛分系统采用了立置环保悬臂筛网振动筛。系统双系列配置,包括进料皮带及对应的振动筛筛分线,可实现两次多粒级顺序筛分。烧结矿通过筛分整粒分为成品烧结矿、铺底料和返矿。两个一次筛之间设有移动溜槽,可将易堵槽的开机料不经筛分直接卸到成品皮带上。
烧结矿出厂前设有全自动取制样检验系统。旋转采样机从成品出厂皮带机头部取得样品,并送到制样楼。采样机旋转截取采用变频无级调速方式,可根据皮带秤信号自动调整,确保每次截取相同质量。制样楼内可自动完成成分试样调制、粒度筛分与粒级计算、转鼓指数测定、物理冶金性能试样收集和弃料回收。
主抽风与除尘系统。
新三烧结主抽风机采用2×30000m3/min(工况)双吸双支撑离心式烧结抽风机,均为引进设备。主抽风机进口负压19.5kPa,全压20kPa,设计效率≥82%。采用变频调速运行,以合理控制风机运行状态,有利于烧结风量调节和能耗降低。配套采用高压异步电机,可节省投资,并方便安装和使用维护。主抽风机变频调速系统采用“二拖二”设计方案,两台变频器可对两台主抽风机的电机进行交叉变频调速,两台变频器互为备用。
主电除尘为2台卧式四电场除尘器,通风截面积560m2,配备16台1.6A/85kV高频电源。输灰系统以一、二电场为回收系,三、四电场为废弃系进行配置。回收系粉尘经气力输送系统返回配料室,废弃系粉尘由真空罐车外运。当气力输送故障或生产初期粉尘过湿时,两个系列的粉尘均可加湿外排。
烟气治理。
新三烧结烟气净化采用活性炭法二级吸附工艺,设计脱硫效率≥95%、脱硝效率≥80%,可实现SO2排放浓度≤50mg/Nm3,NOx排放浓度≤110mg/Nm3,颗粒物排放浓度≤20mg/Nm3,二英排放浓度≤0.5ng-TEQ/Nm3。
烟气净化设施主要由烟气系统、吸附系统、解吸系统、活性炭输送系统、活性炭卸料存贮系统等组成。经过烟气混匀器后,主抽烟气分成两路分别进入净化系统。每一路混匀烟气被调节至135℃以下,先后经过两级吸附塔,每级吸附塔前均配有相应的增压风机。吸附塔入口前喷入氨气,烟气依次经过吸附塔的前、中、后3个通道,SO2、NOx、二英、重金属和粉尘等污染物被活性炭层吸附,或经催化反应生成无害物质,净烟气由主烟囱排放。活性炭由吸附塔顶加入,借助重力和塔底出料装置向下移动。吸附污染物的活性炭进入解析塔,在400℃以上解析出富硫气体SRG,并被送往制酸系统制成硫酸。小颗粒活性炭粉送入粉仓,用吸引式罐车运输至高炉系统作为燃料使用。
余热回收。
新三烧结的环冷热废气经优化设计得到充分回收利用,包括点火助燃、余热锅炉产蒸汽、低温余热ORC发电和返烧结利用四部分。
环冷机约300℃高温废气用于点火助燃及热风保温,风量为12.84万标准立方米/小时。环冷机高温段(1号、2号烟囱)热废气约108万标准立方米/小时,经直联炉罩式双压余热锅炉回收热能产生蒸汽,降温后废气返回环冷机重新利用。环冷机中低温段(3号烟囱)热废气约60万标准立方米/小时,采用低温余热ORC发电技术回收热能,余热回收后的废气与低温段(4号烟囱)约60万标准立方米/小时热废气通过风机一并返回烧结机台面上的烟气罩。另有剩余低温废气约40万标准立方米/小时,通过双层阶梯人形罩降尘后外排,并满足无组织排放要求。
环境除尘。
新三烧结对生产过程各产尘点、产尘设备和转运环节采取综合有效措施,控制粉尘扩散外逸,对废气进行净化处理,确保环境除尘系统的袋式除尘器废气排放浓度≤20mg/Nm3。主要设计措施如下:
一是采用高效率的长袋脉冲除尘器为净化设备,以进口脉冲阀和脉冲控制仪直接控制清灰,配套设置粉尘监控仪,脉冲控制仪与粉尘监控仪配合使用,可精确判断滤袋的好坏状态;有针对性地采用防静电覆膜滤料、150℃高温覆膜滤料和普通覆膜滤料。二是在强力混合机和二次混合机排料端各设置1台塑烧板除尘器,以处理混合制粒过程中产生的含湿废气。三是充分回收利用各类除尘灰。燃料系统除尘粉直接进入配料室燃料槽,塑烧板除尘器收集的粉尘直接返回工艺流程,其他除尘灰和主电除尘灰采用气力输送方式回收。四是采用先进的除尘管道阻力平衡专利技术,有效避免各分支管阻力平衡失调,确保系统运行可靠。风量较大的重要除尘点支管上在设置阻力平衡器基础上增设1个手动蝶阀,以便异常工况时调节抽风量。
在烧结工序升级改造过程中,宝钢股份积极采用新工艺新装备新技术,形成了烧结生产典型工艺流程,将促进宝钢打造示范性样板烧结工厂。宝钢四烧结投运以来,烧结生产逐渐稳定,产量、质量、能耗和排放均已达到良好水平,详见附表。
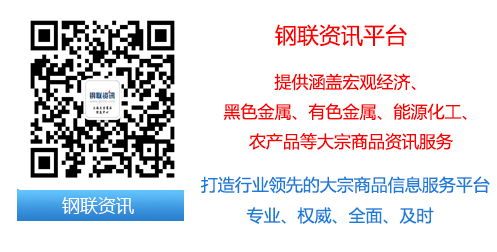
[查数据、做研究,上钢联数据]